
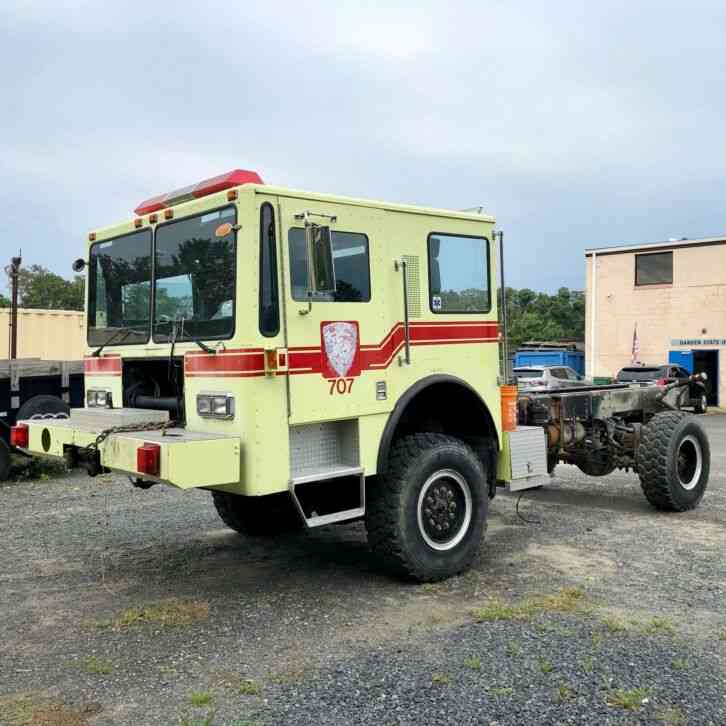
The use of the hunter/killer concept allowed both the gunner and the commander to contribute as much information as possible towards the neutralization of the enemy.

The man-machine interface for the HSTV(L) was of prime importance. The track was an improved version of the type found on the M551 Sheridan. A 355.6 mm jounce and 127 mm rebound travel was possible due to the small 558.8 mm diameter road wheels. Teledyne supplied the fixed height hydro-pneumatic suspension system. The hydraulic pump supplied power for the engine compartment mounted oil cooler fan and through a hydraulic slip ring it also supplied power to the gun control system and automatic ammunition loader in the turret. Auxiliary power was provided by two 250 amp generators and a 60 gpm hydraulic pump.

The transmission was an X-300 Detroit Diesel Allison automatic four-speed with lock-up torque converter. Avco Lycoming supplied the non-regenerative 650 horsepower modified helicopter gas turbine. Propulsion for the HSTV(L) came from a gas turbine engine mounted beside the transmission with a cross-drive gearbox connecting the two. Cadillac Gage supplied the gun control and stabilization system for HSTV(L). Fire-on-the-move capabilities were improved by decoupling the yaw motion of the hull from the turret. Automatic tracking and rate aid tracking could also be accomplished by the fire control processor.īoth elevation and azimuth stabilization was provided for the 75 mm gun with a slaved killer sight and an independently stabilized hunter sight. The laser rangefinder was supplied by Raytheon.
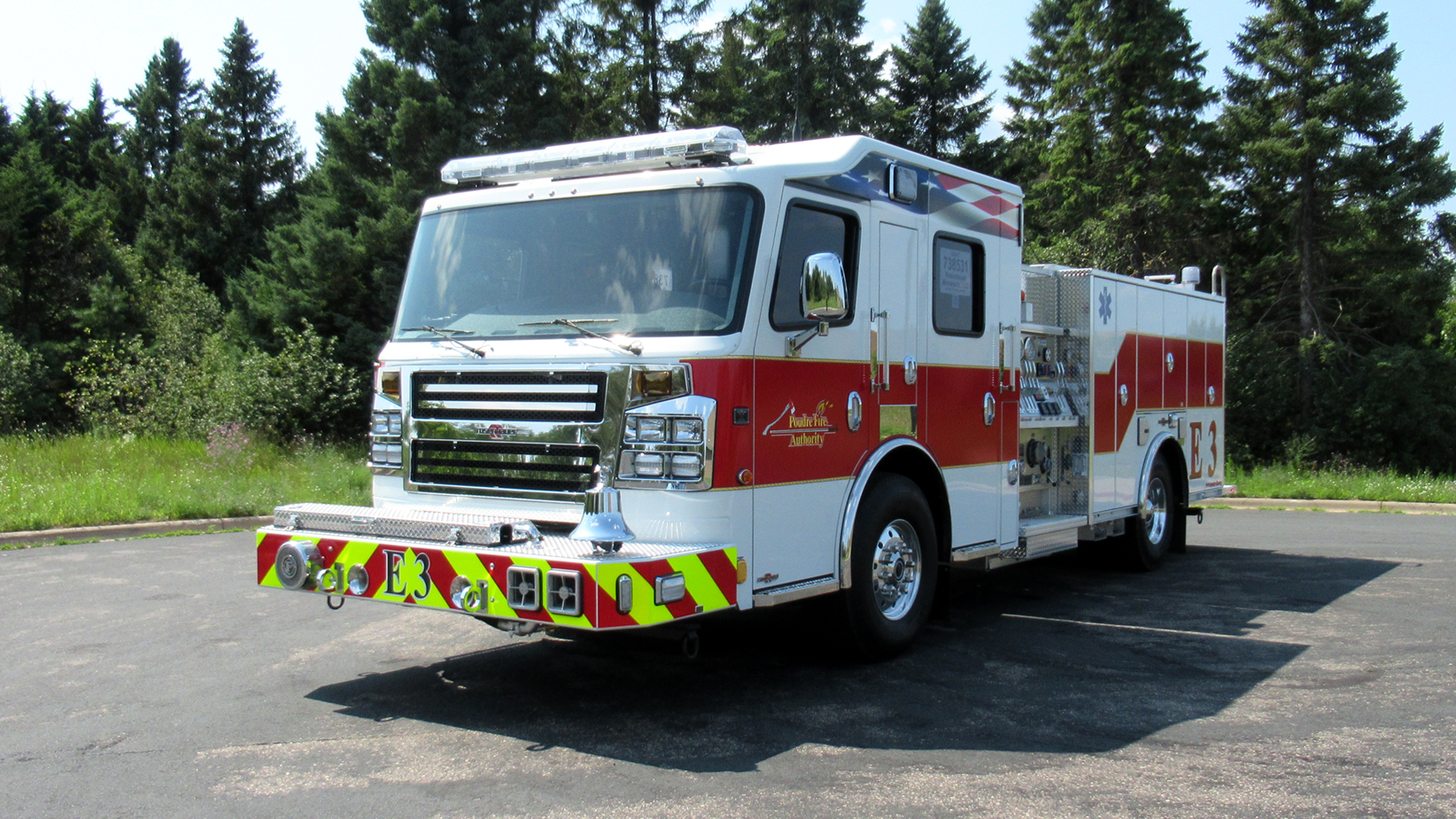
The electronic fire control processor used inputs from the sights, crosswind sensor, muzzle reference, vertical reference system, and an eye-safe CO2 laser rangefinder to compute proper gun pointing.
#Detroit diesel fire commander 11 driver
In the hull, a video screen visible to both gunner and driver received transmissions from hunter and killer sights. The commander could use either a binocular direct view optic eyepiece for improved clarity and reduced power drain, or a video screen. Both direct vision and FLIR (Forward Looking Infra-red) optics were available for either sight. The gunner could then destroy the selected target while the commander returned to search with his hunter sight. Once a target was selected on this sight, the turret and killer sight would be aligned with it. The commander used a stabilized hunter sight that revolved independently of the turret. Texas Instruments supplied the fire-control system which used the hunter/killer concept. The 75 mm gun and automatic ammunition feeder were designed and made by ARES Inc, Port Clinton, Ohio. The in-battery-firing recoil mechanism had a fixed piston that allowed the greater mass of recoil cylinder and breech mechanism parts to recoil during firing. The cannon employed a revolving breech and telescoping ammunition which enabled the automatic loader to load one round per 11/2 seconds. Any crewman could shoot and both hull crewmen could drive.Īlthough a test vehicle, the HSTV(L) was not a variable parameter test bed but an exercise in system realism for the three-man crew, hunter/killer fire control concept and low silhouette.Īrmament for the HSTV(L) consisted of a 7.62 mm M240 machine gun for both commander and coaxial position and a 75 mm smooth bore cannon. The high survivability of this vehicle was derived from the low silhouette, high horsepower per ton, duplication of sights, improved night vision capabilities, and the lack of specific driver and gunner controls. These tests began in September 1982 and continued for about one year. The TACOM Motion Base Simulator, a huge shaker table, was used to provide terrain input. Various stabilization control algorithms were tried along with different combinations of transducers to determine effects on gun pointing performance and the possibility of eliminating some of the expensive sensors such as gyros. Stabilization processing was converted from analogue to digital. The High Survivability Test Vehicle – Lightweight (HSTV-L) was developed under the direction of the TACOM project manager for Armored Combat Vehicle Technology at the US Army Tank-Automotive Command, Warren, Michigan.įollowing the field testing, the HSTV(L) was used for experiments in fire-control and stabilization. The following information has been copied from Jane’s Light Tanks and Armored Cars 1984 by Christopher F. So please excuse the fact that for some unknown reason a truck tire has been placed on the top of the vehicle. Note: I wish I had been able to do some cosmetic work on this vehicle before I photographed it but one of the restrictions I had to agree to in order to get the permit was that we could not get on, or in, or do anything to the equipment.
